Pharmaceutical industry is highly competitive, with stringent regulatory requirements, heavy investments in research and development, and regular changes in medical requirements and the impact of patent rights. Therefore, even minor inaccuracies in business processes and lack of flexibility may result in enormous costs and fines.
Process automation helps pharmaceutical companies mitigate the risk of errors and ensure compliance with quality standards. In addition, automation provides up-to-date, complete and reliable data on production, supplies, inventories, sales, competitors.
This article will tell you what processes a pharmaceutical company can automate and its subsequent benefits.
Table of Сontents
- Reasons for Automation for a Pharmaceutical Company
- Business Processes Automated by Pharmaceutical Companies
- Keep an eye on your shelves. Try Goods Checker!
- How Automation Helped Monitor Pharmacy Shelves and Improve Planograms
- Accuracy, Speed and Quality in All Business Processes are What Automation Gives to Business
- FAQ
Reasons for Automation for a Pharmaceutical Company
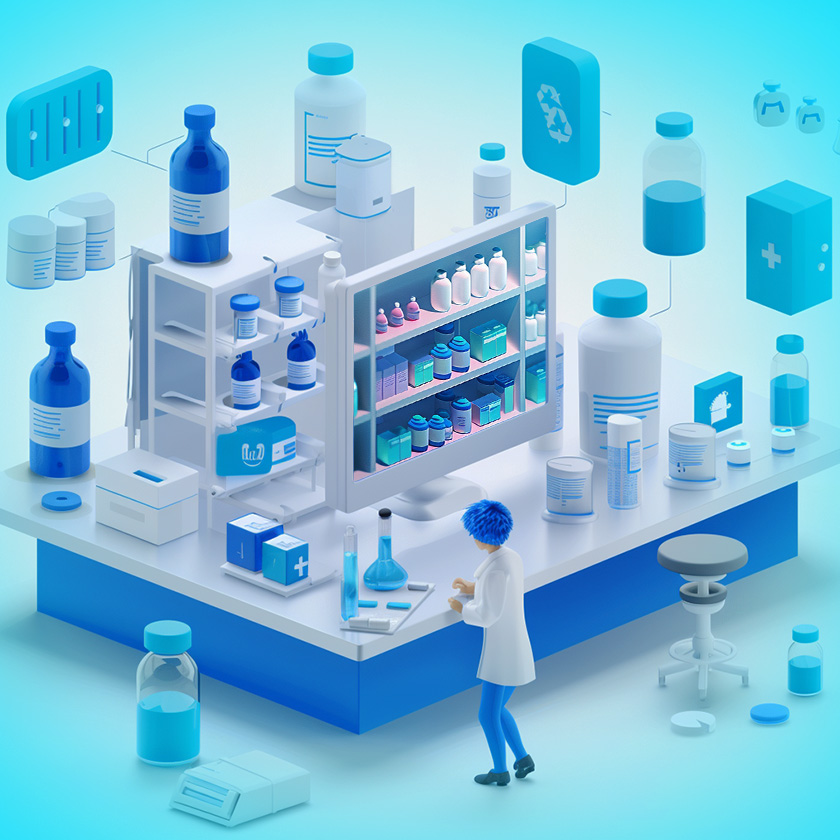
Automation helps companies improve the quality and reliability of manufacturing processes, meet stringent statutory requirements, conduct clinical trials and develop formulations faster, improve marketing strategies and personalize advertising.
In pharmaceutical manufacturing, automation significantly reduces the probability of errors in complex processes. For example, a manual production report may contain errors in raw material or process data. This leads to wrong conclusions, loss of time and money searching for and correcting errors. An automated system prevents such inaccuracies and ensures reliability of analytics.
Automation also expedite business processes, making it possible for pharmaceutical companies to rapidly respond to market changes. In long term perspective, this reduces operating costs due to resource optimisation, reduced number of rejected and expired products and improved supply chain management.
Products traceability from raw materials to the consumer is crucial. Automated tracking and serialisation systems help to identify any counterfeit products and to recall any batch where necessary. In addition, automation enhances process transparency, providing management with current data to make informed decisions.
Business Processes Automated by Pharmaceutical Companies
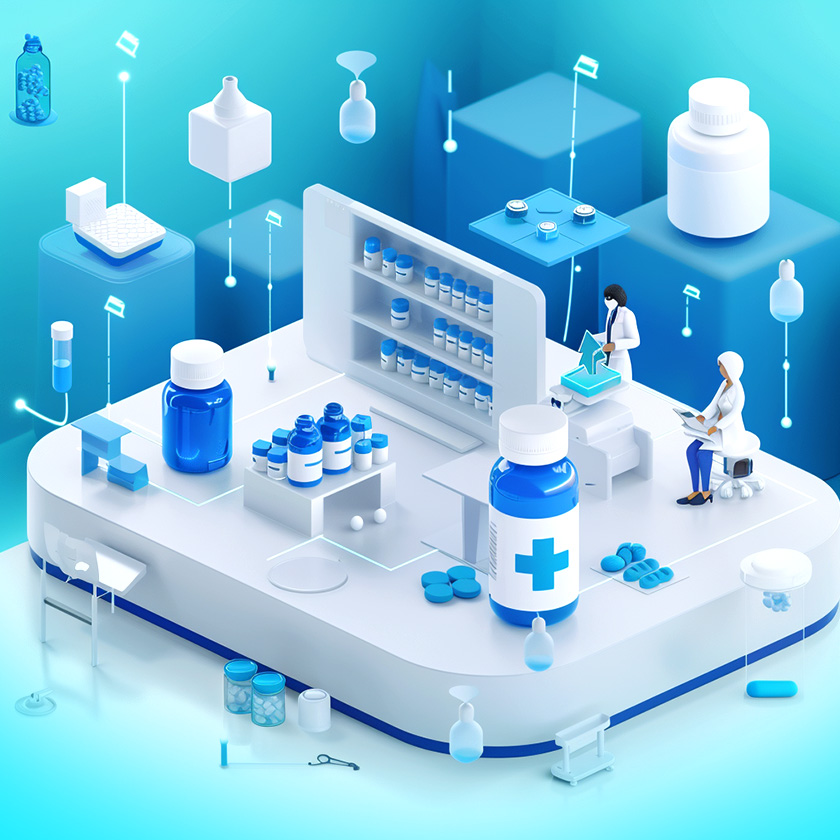
Merchandising and Sales
Proper display and sales management are as important for pharmaceutical companies as research, production or logistics, because each company competes for consumers. In order for the buyer to catch a sight of the product, it is necessary to understand where this product should be placed on the shelf, and what medicines, vitamins or POS materials should be arranged nearby. In addition, you need to make sure that the product is always not only in stock at the pharmacy, but also displayed on the shelf on time.
Automation of sales analysis and display monitoring addresses these tasks. BI systems are able to quickly and comprehensively analyze all available data and visualize trends in demand and sales. This helps better understand people’s needs and tailor your marketing and sales strategies.
The source data must be up-to-date and reliable so that BI systems perform analysis correctly. Such data are obtained with the help of automated point of sale audit and display analysis. For instance, merchandise display control using Goods Checker, an IT solution based on computer vision, helps to quickly check the placement of products, price tags and POS materials according to the planogram.
The Goods Checker system identifies products from different manufacturers, including competitors, and tracks changes in the product display. It works like this: medical representatives take photos of shelves with drugs in a pharmacy, and Goods Checker processes the images and provides marking for each photo. The processed image shows which drugs are placed correctly and which must be rearranged.
Goods Checker also generates analytical data with the parameters required for the business: share of the brand and competitors on the shelves, reasons for non-compliance with the planogram, dynamics of product representation, performance of representatives, etc. Data can be provided with the breakdown by regions, types of pharmacy and periods to identify trends.
Due to automation, managers obtain quick feedback. If any problems with the merchandise display are identified, and the medical representative is not able to eliminate them, they simply leave a comment on the photo stating the reason. This helps to rapidly identify and resolve any problems with the product display, increasing merchandising efficiency.
Such approach ensures a clear understanding of the situation on the shelves, shows cases when a product is unavailable and helps to make decisions on product range optimisation and promotion strategy.
Logistics and Supply Chain
Pharmaceutical companies need timely and accurate information about the status, timing and location of products, and maintain strict records of deliveries to comply with regulatory requirements. Therefore, it is important for pharmaceutical companies to supervise all logistics processes. Inaccuracies in contract management and insufficient performance monitoring may result in supply chain disruptions and therefore increased costs. Automation helps build transparent and controlled logistics, accurately identify medicines and know where they are at any time.
In addition, it is essential for companies to be able to forecast consumer demand in order to maintain a balance between production and inventory. After all, pharmaceutical products have a limited shelf life, so pharmaceutical companies must understand how much raw material they need to produce the required amount of medicine.
Safety and Production
Manufacturing processes in the pharmaceutical industry are complex and highly demanding, as even minor deviations can have serious consequences for patient health.
Automation helps to oversee, document and manage production processes by tracking each stage: from loading raw materials to finished products. Technologies make production and business processes transparent and integrated, help streamline them and minimize the probability of in-process errors.
In addition, automated systems help monitor the safety of employees at work. The systems keep track of the availability of personal protective equipment; monitor the indoor climate and other safety aspects. This helps reduce the risk of job-related accidents, ensure smooth production and avoid legal consequences.
Research and Development
During research, personnel process enormous amounts of information. Often conventional analytics systems can no longer quickly cope with this flow of data. Artificial intelligence systems accelerate the analysis of large volumes of clinical, demographic, and laboratory data. Solutions using advanced statistical methods, machine learning and neural networks help identify important patterns and speed up the process of researching new drugs.
Automation makes it easier to conduct tests and experiments. It eliminates errors due to fatigue or inattention of employees, or the influence of external factors, which also speeds up the process and reduces costs. In addition, artificial intelligence processes and evaluates information about side effects from medication faster. Therefore, companies can quickly address undesired effects.
Keep an eye on your shelves. Try Goods Checker!
Automate shelf monitoring. Get clear analytical reports. Start your project quickly.
Leave your contacts and we will get back to you within 24 hours.
How Automation Helped Monitor Pharmacy Shelves and Improve Planograms
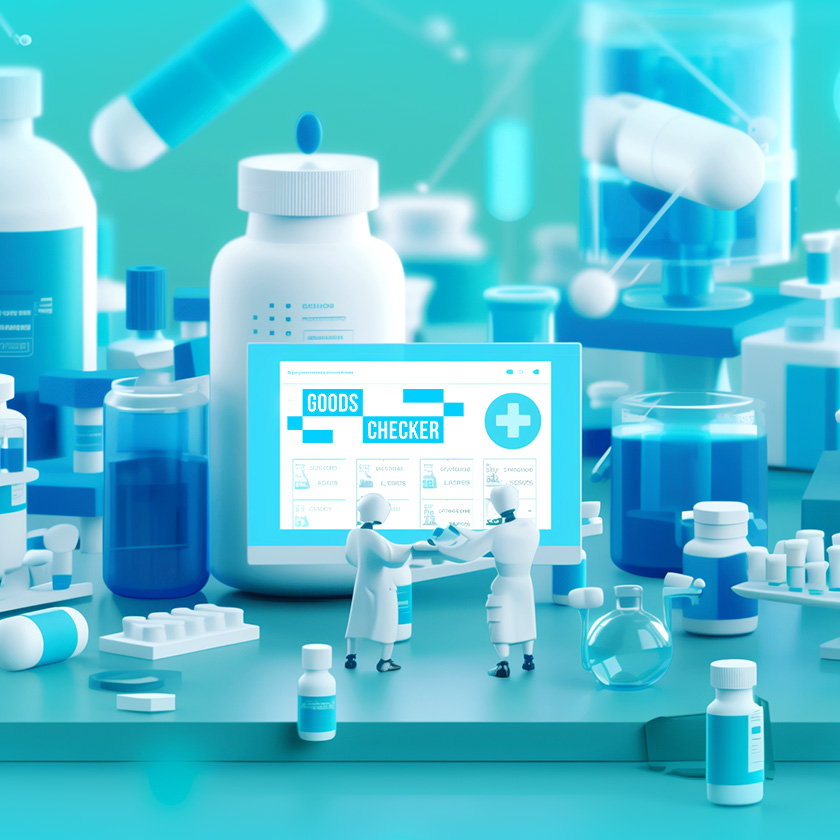
Display Monitoring
Drug manufacturer was faced with the need to monitor the display of goods in pharmacies in Kazakhstan, Uzbekistan and Kyrgyzstan. Currently, medical representatives manually check the layout for compliance with the planogram, which is time-consuming and often leads to errors.
To address this challenge our client chose the Goods Checker IT solution powered by computer vision. The mobile application allows the customer’s medical representatives to quickly compare the layout against the planogram and identify inconsistencies. Recognition accuracy is over 90%, and the time spent on pharmacy visit does not exceed five minutes.
The Goods Checker web application immediately processes data from medical representatives’ visits and generates detailed analytics for customer managers. The application provides information on compliance with planograms in various regions and cities, shelf share, availability of POS materials and other important metrics.
The pilot project has confirmed the efficiency of the solution: now it takes less than five minutes for a medical representative to visit a pharmacy. The customer has seen for itself that it required less time for its employees to visit to a pharmacy and managers are able to obtain reporting data in a timely manner.
Moreover, Goods Checker automatically processes thousands of images daily, allowing medical representatives to focus on more important tasks. Due to automated checking, errors typical of human merchandise display control are virtually eliminated completely, since computer vision recognises products with 95% accuracy.
Based on the collected data, the system generates detailed reports on product availability, compliance with standards and the performance of medical representatives. Goods Checker is integrable with other business programs, which makes it possible to collect information on a centralised basis. Built-in analytics provide detailed information on product representation, as well as KPIs for medical representatives and pharmacies.
Planogram Improvement
A major chain of pharmacies in Eastern Europe has about 1,400 points of sale, where they sell from 1,000 to 1,500 types of medicines, dietary supplements and other items.
To increase turnover and reduce the number of situations where goods are out of stock on the shelf, they decided to automate the creation of planograms and receive feedback on their compliance from employees in pharmacies. Analysis of such data will help identify bottlenecks in the preparation of layouts and planograms and streamline the process.
During the project, we created planograms for all pharmacies, configured the exchange of information with the accounting system and regular distribution of planograms for employees to complete tasks.
As a result, the pharmacy chain improved category management, visual presentation of products to customers and reduced the number of out-of-stock items.
Accuracy, Speed and Quality in All Business Processes are What Automation Gives to Business
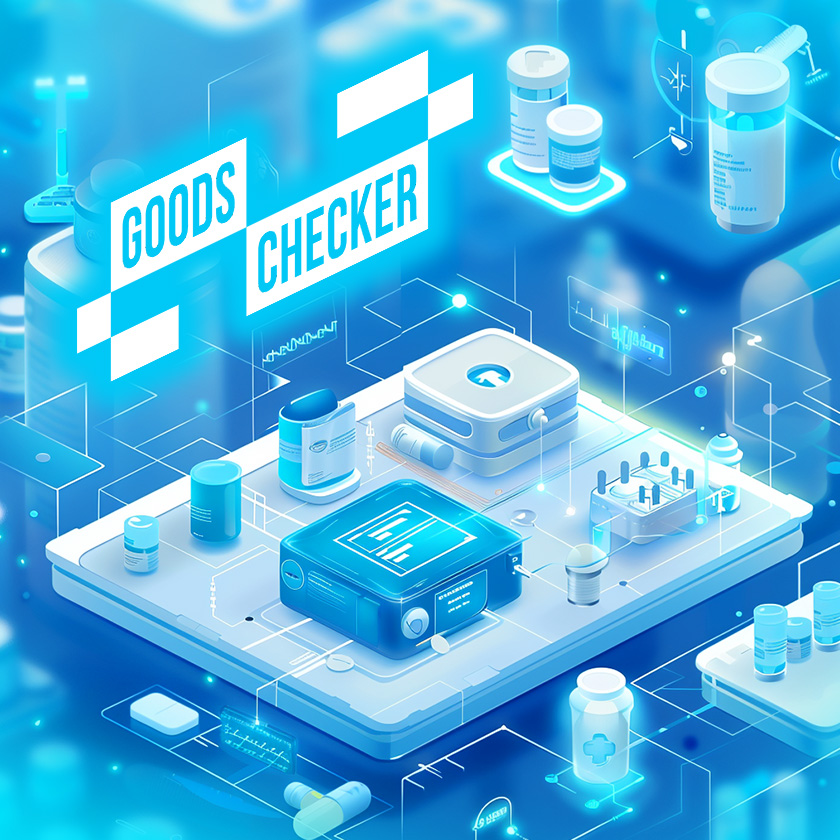
Prompt adaptation to changing market conditions is becoming a key factor in the successful operation of a pharmaceutical company.
BI systems, artificial intelligence and other technologies help improve business processes: make them faster, more transparent and integrated. All this becomes the basis for collecting complete, reliable and up-to-date data, from which managers extract valuable information for making strategic decisions and ensuring competitiveness in the market.
Today, automation for pharmaceutical companies is the critical factor that helps improve the quality and safety of products and drive visibility against competitors.
FAQ
Automation ensures transparent and controlled logistics by tracking medicine locations, timestamps, and delivery status. It helps prevent supply chain disruptions, reduces costs, and ensures compliance with strict regulations.
Automated systems monitor every production stage—from raw material loading to packaging—making processes transparent and integrated. They help document and manage operations, minimize in-process errors, and even track employee safety measures like PPE usage and indoor climate conditions.
AI and automation accelerate data processing in R&D by quickly analyzing clinical, demographic, and lab data using machine learning and neural networks. Automated testing reduces manual error, speeds up experiments, and enables faster detection of medication side effects.
In countries like Kazakhstan, Uzbekistan, and Kyrgyzstan, medical reps previously checked shelf layouts manually. Automation of planogram creation and compliance feedback reduces out-of-stock instances and optimizes product placement in pharmacies.
Automation fosters faster adaptation to market changes, greater transparency, integration of processes, and the generation of reliable and up-to-date data. These benefits support strategic decision-making and help pharmaceutical firms remain competitive.