Identification of Errors in the Display of Premium Goods by the Distributor
Business Challenge
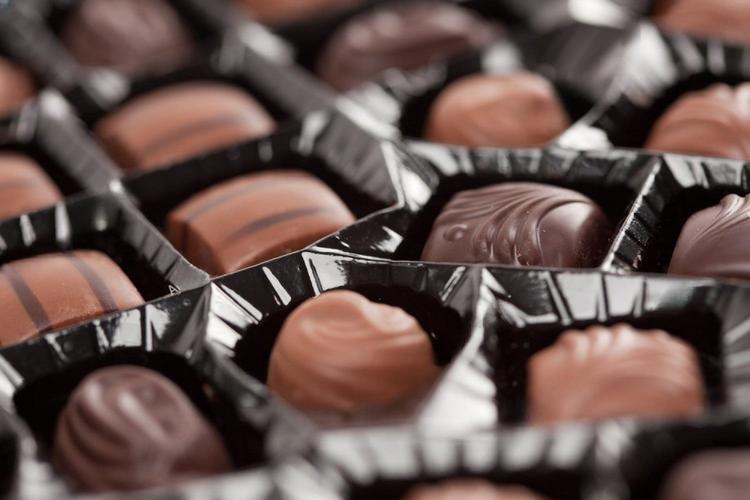
Customer
The customer is a large multi-brand distributor of chocolate, candies, tea, coffee, spices and other food products. It has been successfully operating in the market since 2000; the company currently employs 2,700 people. It uses the services of both its in-house auditors and merchandisers of its partner retail chains. Currently, the customer uses a special application for merchandisers in its operations, but its functionality does not cover all tasks: the application cannot recognize products and check planograms.
Challenge
Working with different retail chains, the customer was faced with the problem of inconsistency between the planogram and the display of goods in retail outlets. It was necessary to promptly provide information to retail outlets about non-compliance with trade and marketing agreements. We decided to use Goods Checker to analyze the merchandiser performance.
Solution
A group of products was chosen for the pilot project: boxes of premium chocolates. For them, it is very important how products are presented on store shelves, since the same high standards must be observed in all countries.
The project lasted 3 months: for 1.5 of them, the developers trained computer vision models and customized the system for the customer, and for another 1.5 months, auditors checked the layout in real-world environment using Goods Checker.
In the course of work, the customer clarified the requirements, and the team added new functionality: for example, they improved the web application to view photos that the auditor uploads to the mobile application.
Highlights
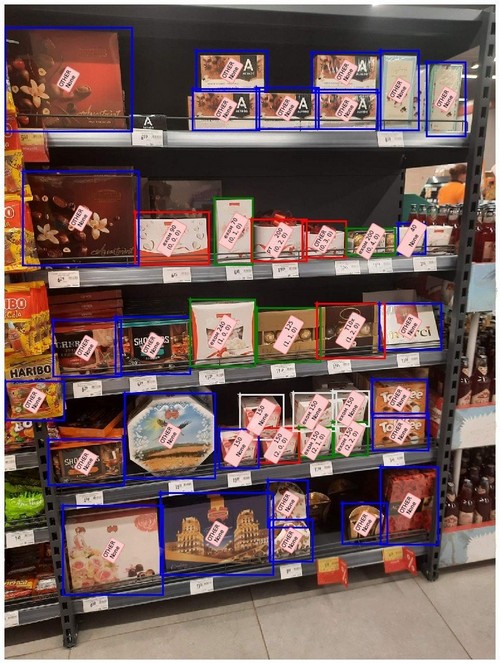
20
planograms
20
SKUs
80
retail outlets in one city
5
mobile app users
Result
Goods Checker solution helped to identify actual violations of the display in the retail chain. The company’s managers received a transparent display monitoring system and were able to improve their cooperation with the chain in terms of product representation.
Planogram compliance rate improved from 60% to 90%. The time for field audits in retail facilities has been reduced due to the high speed of Goods Checker: one image is processed in up to 30 seconds. The final recognition accuracy is 90%.